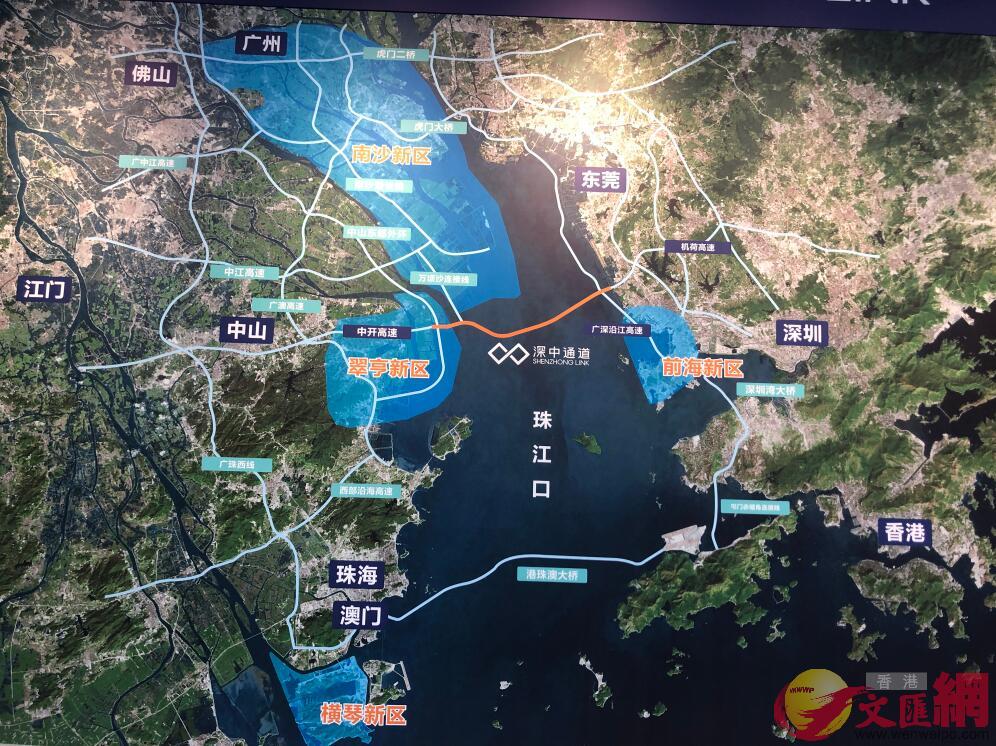
記者早前到訪深中通道管理中心,該中心展示深中通道與港珠澳大橋的位置示意圖(方俊明 攝)
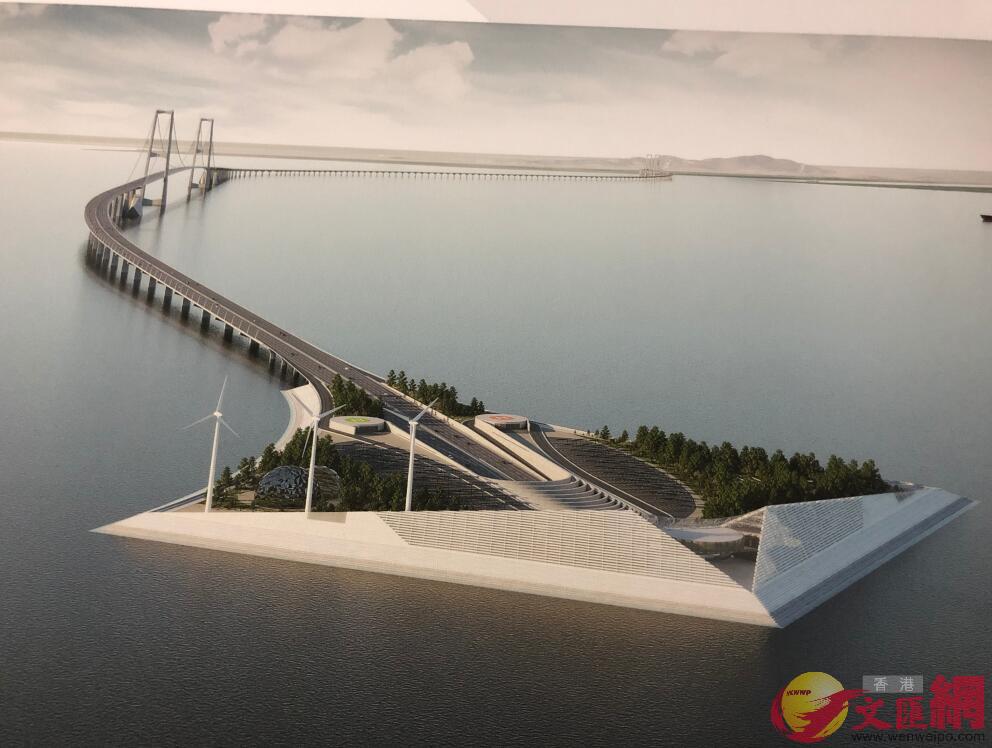
深中通道是集「橋、島、隧、水下互通」於一體的世界級集群工程,圖為深中通道管理中心展示的設計圖(方俊明 攝)
【文匯網訊】(香港文匯網 記者 方俊明)大灣區交通重點樞紐工程「深中通道」目前進行最難的沉管隧道建設。深中通道管理中心有關負責人9日受訪透露,繼首個管節(E1管節)鋼殼在6月下旬從南沙龍穴島船廠運抵珠海牛頭島預制廠後,目前進入E1管節混凝土澆築階段。據悉,該預制廠曾承接港珠澳大橋33節隧道沉管建造,經過11個月的升級改造並獲得11項專利,打造成更加智慧化的「夢工廠」。其中,幾乎所有生產的數據都可在一塊大屏幕上輕鬆捕捉,具備每個月生產一節管節的能力,比港珠澳大橋提升了一倍多;而相比港珠澳大橋E1管節從預制廠搬移到淺塢區花了1個多月,如今最快提升到3個小時,深中通道建設工效較港珠澳大橋大幅提速。
據瞭解,深中通道隧道沉管的生產全部採用「工廠法」流水線法,沉管管節首先在廣州南沙龍穴島船廠完成鋼殼的製造,後運抵珠海牛頭島預制廠進行混凝土澆築,在淺塢區、深塢區完成一次舾裝和二次舾裝作業後,再運至隧址進行沉放。
單個沉管排水量相當於中型航母
深中通道沉管隧道長6.8公里,是世界首例雙向八車道海底沉管隧道,其斷面寬度達46米到55.46米,比港珠澳大橋雙向六車道鋼筋混凝土沉管隧道斷面還要寬9米,單孔跨度超過18米,沉放最大水深達到40米,沉管結構的受力非常複雜,是目前世界上最寬的海底沉管隧道。

深中通道首節沉管計劃今年底安放,整個通道工程擬2024年建成通車,圖為工程建設現場(方俊明 攝)
在深中通道隧道建設過程中,將由33個標準管節「搭積木」般連接而成,每個標準管節的尺寸為165×46×10.6米,用鋼量約1萬噸,其排水量相當於一艘中型航空母艦。而相比港珠澳大橋6年建設33個管節,改造後的預制廠將要在3年內完成深中通道33個管節中的22個任務,對預制廠的設備與工藝提出更高要求。
「目前,沉管預制廠全面『智慧化』升級改造歷時11個月已完成,期間進行了80多次方案研討、300多份圖紙、23項攻關,具備每個月生產一節管節的能力,比港珠澳大橋提高了一倍多。」深中通道管理中心有關負責人表示,工程師們通過上百次的科研試驗,突破了國際技術封鎖,配製出更適合鋼殼沉管澆築、且穩健性更強的「高流動性自密實混凝土」,並研發出智能澆築系統。「該智能系統可通過對混凝土生產及澆築等全過程監控,實時記錄統計數據,不需要人工去做任何操作,包括作業人員所有的信息均可在手機上查得到看得到」。
鋼殼沉管隧道「全球體量最大」
作為粵港澳大灣區兩大「超級工程」,深中通道與港珠澳大橋經常被坊間「一比高下」。深中通道管理中心有關負責人指出,相比港珠澳大橋沉管隧道「矩形箱式鋼筋混凝土結構」,深中通道在國內首次採用「鋼殼混凝土結構」是最大的創新,也是整個工程的最大挑戰之一。而深中通道隧道是目前全球最寬、體量最大、施工難度極高的鋼殼沉管隧道。
該負責人表示,深中通道鋼殼沉管寬度約為日本的1.5倍,用鋼量達32萬噸,如此大規模、大體量地使用鋼殼沉管在全球尚屬首例,該工程的設計和建造沒有現成標準;建成後,它將建立完整的世界上最寬最大規模的鋼殼沉管隧道技術體系和標準,成為行業的標桿。
深中通道沉管隧道5大挑戰
一,超寬:隧道採用雙向8車道技術標準,管節斷面寬度46米,為世界首例,設計及施工難度大。
二,變寬:隧道設置615米的變寬段,即由雙向8車道加寬至雙向12車道;管節斷面寬度由46米變寬至約70米,在隧道內多次分合流。
三,深埋:沉管隧道埋置深度深,最深位置沉管底標高距水面接近40米,管節結構設計難度高。
四,回淤量大:洪季回淤強度平均接近2厘米/天,颱風期最大回淤強度超過5厘米/天,沉管沉放及沉降控制難度大。
五,挖砂坑區域地層穩定性差:西島斜坡段位於超大挖沙坑內,區域地層擾動嚴重,穩定性很差,對基槽開挖成槽造成較大困難。
深中通道帶來行業標準化、智能化升級
一,深中通道預制廠幾乎所有生產的數據都可在一塊大屏幕上輕鬆捕捉,具備每個月生產一節管節的能力,比港珠澳大橋提升了一倍多。
二,通過上百次的科研試驗,突破了國際技術封鎖,配製出更適合鋼殼沉管澆築、且穩健性更強的「高流動性自密實混凝土」。
三,研發出智能澆築系統,通過對混凝土生產及澆築等全過程監控,實時記錄統計數據,不需要人工去做任何操作。
四,深中通道與廣船國際合作建成鋼殼智能製造「四線一系統」,提早實現了內地造船業界智能打砂和塗裝及大工件機器人焊接的夢想。
五,深中通道隧道將建立完整的世界上最寬、最大規模的鋼殼沉管隧道技術體系和標準,成為行業的標桿。
六,全球首艘沉管浮運安裝一體船「一航津安1」已出塢,相比港珠澳大橋採用的分體式浮運安裝船組,施工效率極大提高。
責任編輯:京辰